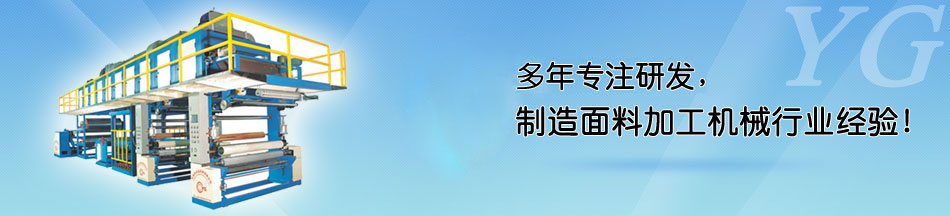
涂布機作為精密涂覆領域的核心設備,其技術演進始終圍繞著涂層均勻性與工藝穩(wěn)定性展開。從熱熔膠涂布到鋰電池極片制造,現(xiàn)代涂布機通過模塊化設計與智能控制系統(tǒng)的融合,實現(xiàn)了從流體控制到成膜質量的全流程精準管理。
熱熔膠涂布系統(tǒng)構成
涂布機的核心工作單元由熱熔膠主機、導流喉管、槍座模塊與涂布槍體構成精密的熱管理網(wǎng)絡。主機采用梯度控溫技術,將固態(tài)膠體加熱至熔點以上 5-10℃,形成具有適當流動性的液態(tài)膠體。經(jīng)初級過濾后,膠液通過恒溫喉管輸送至槍座模塊,此過程溫度波動控制在 ±1℃以內,確保膠液粘度的穩(wěn)定性。
槍座模塊內置二級過濾裝置,可攔截直徑大于 50μm 的雜質顆粒。針對不同涂布需求,該模塊集成壓縮空氣加熱功能,當采用噴霧涂布時,可將壓縮空氣升溫至 80-120℃,防止膠液接觸冷空氣時發(fā)生局部凝固。槍體作為終端執(zhí)行機構,配置有螺旋噴槍、Z 型刮刀等 12 種可更換噴嘴,適應從微米級點膠到連續(xù)面涂的多樣化工藝要求。
流體動力學控制技術
刀刮涂布與輥涂構成兩種基礎涂布機理。刀刮系統(tǒng)通過納米級間隙調節(jié)機構,可實現(xiàn) 5-500μm 涂層厚度的精確控制。當基材以 0.5-30m/min 速度通過時,精密刮刀將多余漿料剝離,形成均勻濕膜。輥涂系統(tǒng)采用三級輥系配置,上涂輥與計量輥的間隙公差控制在 ±2μm,配合 20-80rpm 的差速調節(jié),有效消除流體邊界效應。
在鋰電池極片涂布領域,設備集成五軸聯(lián)動補償系統(tǒng)。DDR 直驅電機驅動的背輥轉速精度達 3‰,配合面密度檢測儀的實時反饋,模頭橫向調節(jié)機構可在 0.5 秒內完成 ±0.1mm 的位置修正。這種動態(tài)補償機制使面密度波動穩(wěn)定在 ±1.2% 以內,遠超傳統(tǒng)機械傳動的控制精度。
智能控制系統(tǒng)集成
現(xiàn)代涂布機的自動補償系統(tǒng)構建了多維度控制閉環(huán)。溫度控制模塊采用 PID + 前饋算法,將 50 米烘箱的溫差波動抑制在 3℃以內。張力控制系統(tǒng)通過磁粉離合器與浮動輥的協(xié)同作用,使基材張力波動不超過 ±3N。視覺檢測單元搭載 2000 萬像素 CCD 相機,可識別 0.1mm 級別的涂布缺陷,并與糾偏系統(tǒng)形成 ±0.3mm 的定位閉環(huán)。
在能效管理方面,設備采用熱泵回收技術,將烘箱排氣熱量重復利用率提升至 65%。伺服電機的智能待機功能可降低 30% 的待機能耗。這些技術創(chuàng)新使現(xiàn)代涂布機的綜合能效比傳統(tǒng)設備提升 40%,單臺年節(jié)電量超過 12 萬度。
工藝適應性拓展
隨著新材料應用的擴展,涂布機正向多功能集成方向發(fā)展。模塊化設計允許設備在 2 小時內完成刀刮與輥涂模式的轉換。雙工位收放卷系統(tǒng)支持 1000mm 卷徑的不停機換卷,配合 MES 系統(tǒng)的智能排產(chǎn),設備利用率可達 92% 以上。針對納米銀線、石墨烯等新型漿料,開發(fā)出低頻脈沖式供料系統(tǒng),有效解決高固含量漿料的沉降難題。
從精密電子到新能源儲能,涂布技術的持續(xù)革新推動著制造業(yè)的升級進程。未來,隨著數(shù)字孿生技術與物理設備的深度耦合,涂布工藝將實現(xiàn)從經(jīng)驗驅動到模型預測的根本轉變,為功能性涂層制備開辟更廣闊的應用空間。